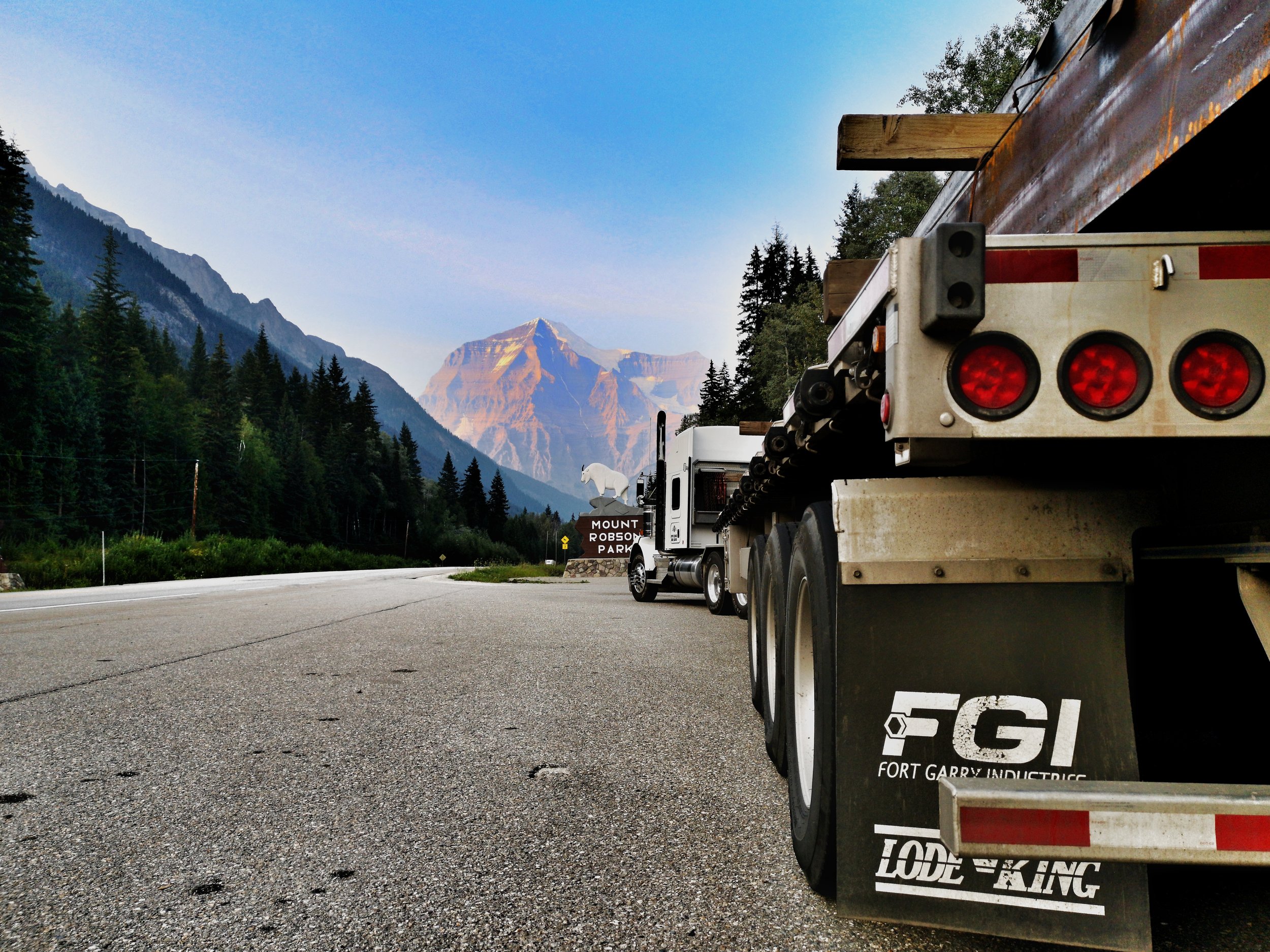
Transportation Compliance Blog

New Manitoba Regulations for Regulated Vehicles: What Carriers Need to Know
Starting July 1, 2025, Manitoba is introducing new marking requirements for regulated vehicles that require a safety fitness certificate to legally operate within the province. This change mandates that these vehicles must display the National Safety Code (NSC) number of the registered owner prominently. This requirement is in addition to the existing mandate for regulated vehicles to be marked with the company logo and/or name….
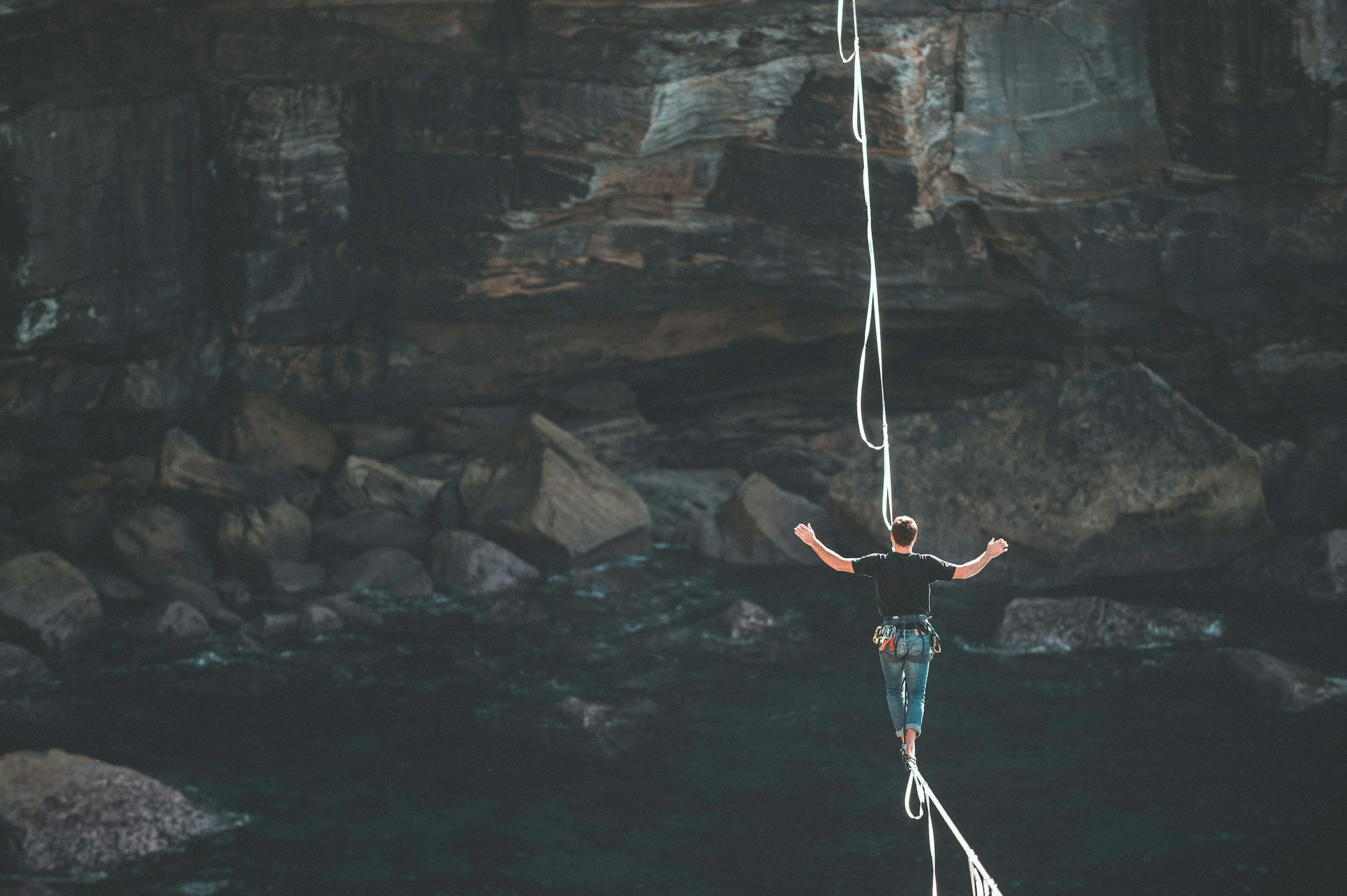
Normalization of Deviation in the Highway Commercial Transportation Industry
Normalization of deviation is a phenomenon where non-standard practices become standard over time within an organization or industry. Initially, small departures from established norms or safety protocols might seem harmless or justified under specific circumstances. However, as these deviations are repeatedly tolerated and go unchallenged, they gradually become the new norm, leading to a culture where deviations are accepted and even expected.
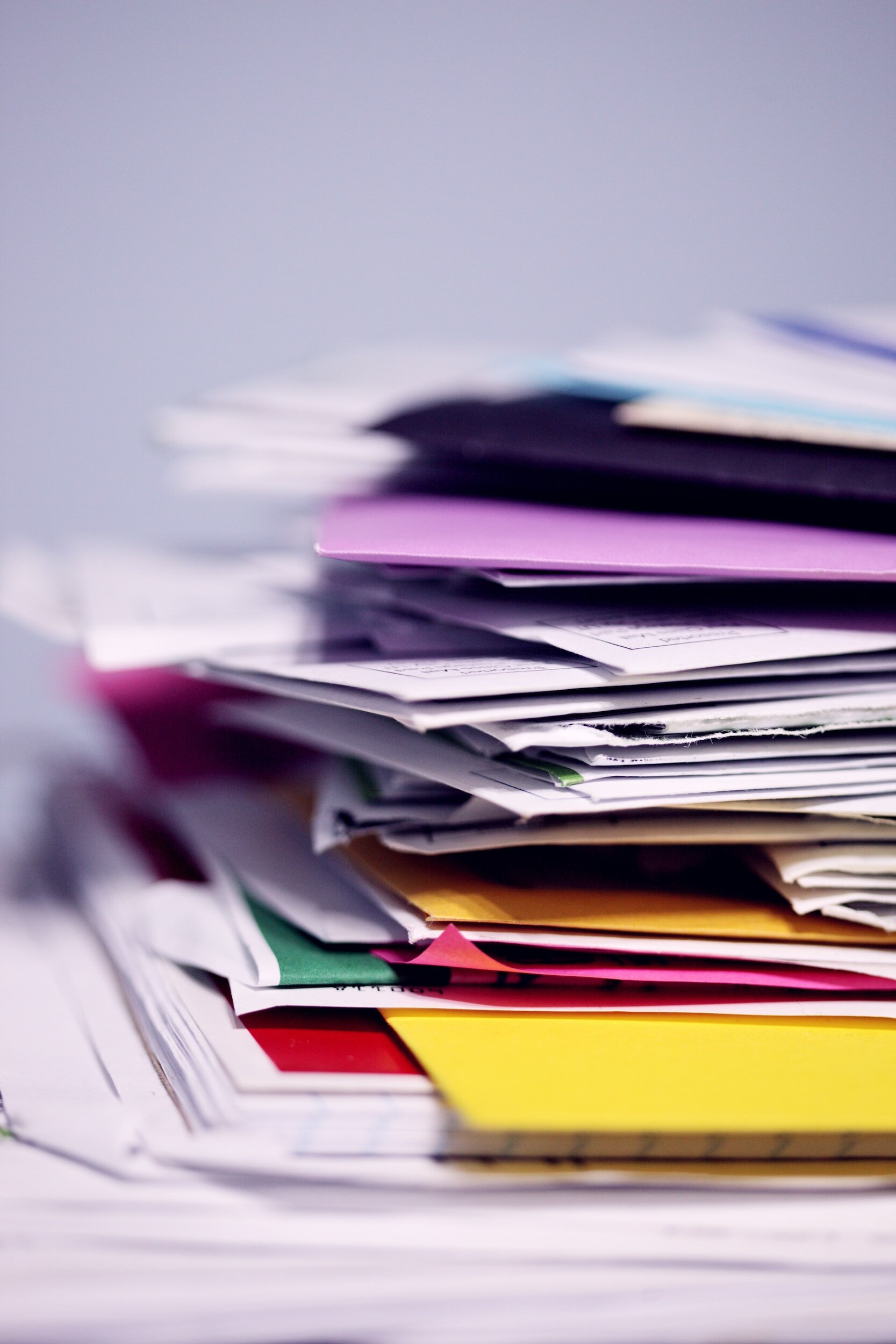
Simplifying ELD Compliance in Canada | Part 1 | ELD Malfunctions
Electronic Logging Devices (ELDs) were introduced to streamline compliance with Hours of Service regulations for commercial carriers while curbing fraudulent practices. However, the current regulations pose challenges for commercial carriers, making compliance near impossible. Let's delve into the issue and explore the complexities surrounding ELD malfunction compliance in Canada.
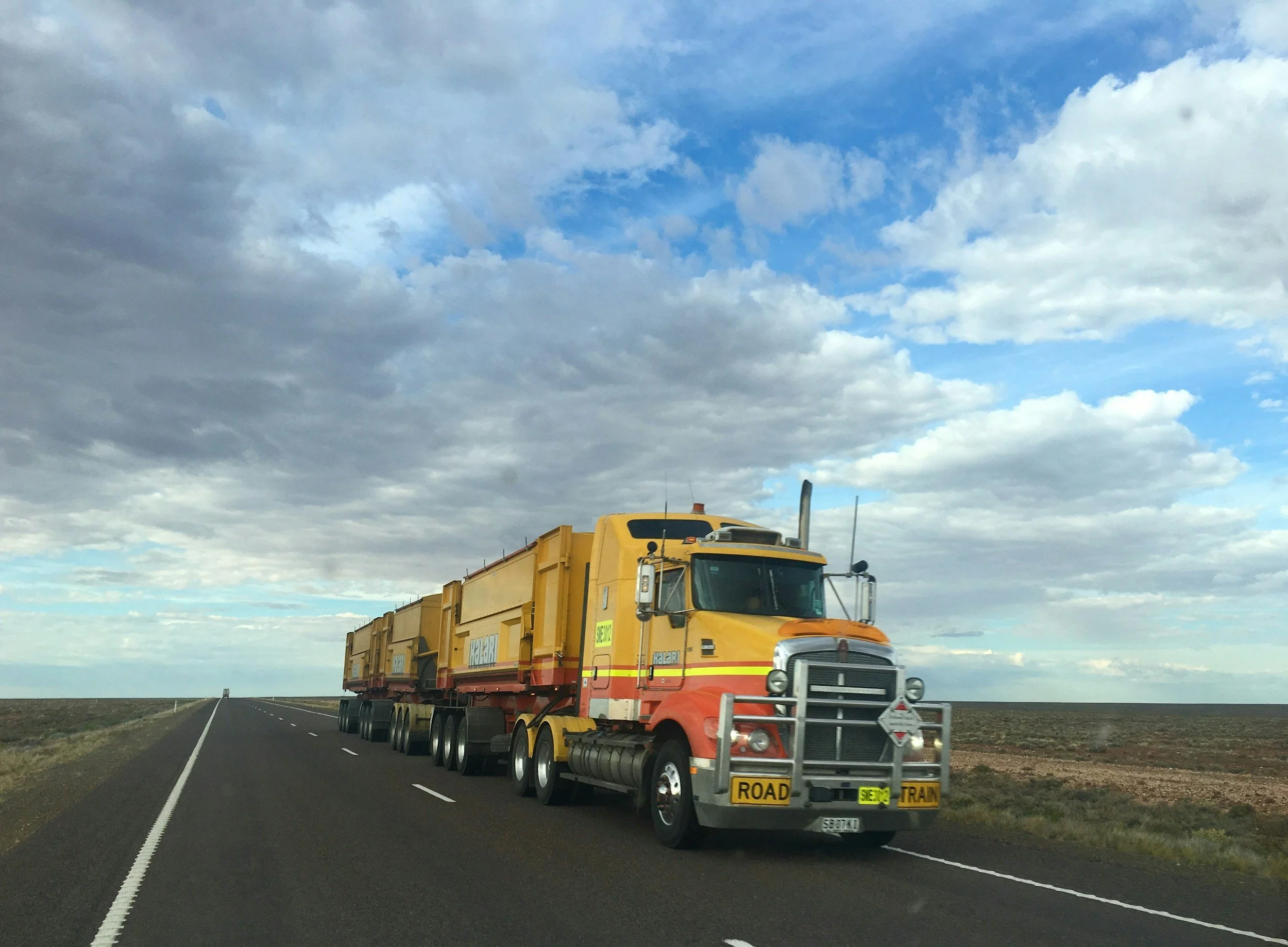
Do you need an ELD?
There are lots of misconceptions around whether or not a carrier is required to have an Electronic Logging Device (ELD) installed in their vehicle(s) as of January 1, 2023 in Alberta. Here’s a quick and easy flow chart to determine your requirements.

Tracking Convictions, Collisions, and CVSA Inspections
Commercial Carriers have a legal responsibility to maintain an accurate record of their drivers convictions of applicable safety laws, administrative penalties, and collisions that are required to be reported to the government…